www.engineering-russia.com
30
'09
Written on Modified on
Tata Steel повышает качество ремонта рельсов при снижении затрат
Tata Steel Rail разработал новую методику экономичного ремонта отдельных дефектов рабочей поверхности рельсов. Ключевая особенность новой технологии состоит в замене ручной дуговой сварки, качество которой часто может быть нестабильным, на автоматические более точные операции. Полуавтоматический процесс использует технологию сварки открытой дугой с трубчатым электродом с низкой температурой предпрогрева для активного руководства преобразованием металла в околошовной зоне. Учитывая то, что средняя цена ремонта или замены короткого участка рельса может достигать нескольких тысяч Евро и что частота появления дефектов контакта колеса и рельса, вероятно, будет увеличиваться с увеличением интенсивности движения на большинстве железных дорог, важность новой ремонтной технологии становится совершенно очевидной. Процесс прошел тщательную отладку и был воплощен в прототипе для демонстрации в реальных условиях на железных дорогах европейских стран, включая Францию и Великобританию.
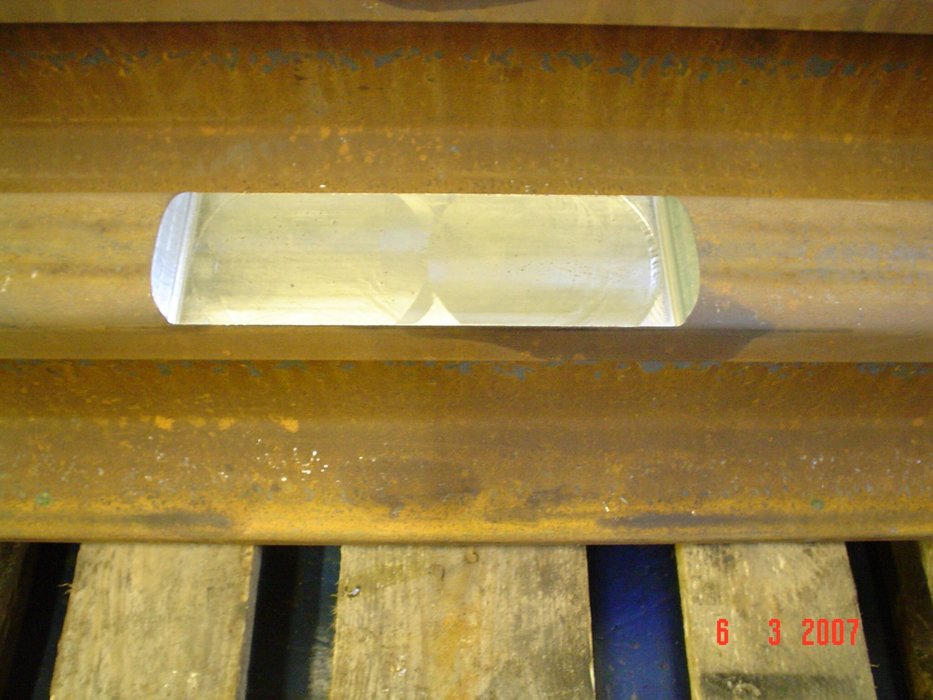
Движение колес вагонов по рельсам создает сложные картины распределения сильных напряжений в месте контакта, что ведет к разрушению поверхности. Широкий диапазон конструкций рельсов, геометрии колес и характера перевозок может приводить к большому разнообразию дефектов поверхности, снижающих ресурс рельса. Такие дефекты как вмятины и термические повреждения от пробуксовки колес появляются даже на самых современных железнодорожных сетях, в среднем можно примерно сказать, что в каждой сети один такой дефект развивается один раз в год через каждые 2 км. Ремонт с помощью замены дефектных участков рельсов дорог и не всегда желателен, так как вносит в участок рельса два разрыва целостности в виде сварных алюмотермических швов (результатов экзотермической реакции, использующей алюминий в качестве восстановителя) и тем самым разрушает преимущества цельнопрокатного рельса, который может достигать длины 120м. Другой возможной альтернативой считалась техника ремонта с помощью ручной дуговой сварки. Несмотря на то, что технология востребована во многих отраслях промышленности, она имеет сильную зависимость от профессионализма сварщика, требует значительного времени и подвержена возможным дефектам, таким как пористость, которая вследствие износа может расширяться и приводить к разрушению рельса, если не будет выявлена ультразвуковым обследованием.
Следующие факторы говорят в пользу экономичности и технической эффективности нового процесса:
1. Уход от обычной температуры предпрогрева в 350°C к уровню 80°C дает преимущество быстроты ремонта, сниженной глубины околошовной зоны и более стабильной микроструктуры.
2. Использование стандартной процедуры удаления дефектного участка с помощью автоматизированного фрезерования обеспечивает повторяемость результата и устраняет субъективный фактор влияния оператора.
3. Использование полуавтоматического программируемого сварочного процесса обеспечивает точное поддержание температуры нагрева и предсказуемую длительность обработки.
Качество восстановленной таким образом рабочей поверхности гарантировано, восстановленное место обладает высокой износостойкостью, аналогичной стандартному рельсу стандарта R260 и однородной твердостью и микроструктурой.
Патентованная технология Tata Steel включает четыре шага.
Сначала дефект удаляется с помощью переносного шлифовального станка, который закрепляется на рельсе. Это обеспечивает полноценное удаление дефектного участка. Само по себе это уже является значительным улучшением по сравнению с использованием ручного шлифовального инструмента или кислородной резки, которые не обеспечивают стабильной формы выборки и качества поверхности, требуемой для автоматической сварки.
Во-вторых, место очищенного дефекта и прилегающий участок подвергается предпрогреву с помощью традиционной горелки. Для рельсов класса 260 температура предпрогрева находится в промежутке от 60 до 80°C. Выбор такого диапазона температуры дает возможность контролировать микроструктуру в прогреваемой зоне и поддерживать запрограммированную квадратную форму стыка слоев последовательных и соседних участков, обеспечивая перлитную микроструктуру в прогреваемой зоне, свободную от мартенситов, повышающих хрупкость. Такая температура подходит для основной массы современных рельсов из высокоуглеродистой стали, но возможно ее следует скорректировать для сталей с другими характеристиками, таких как низкоуглеродистые безкарбидные бейнитные стали.
Третья стадия заключается в использовании полуавтоматического сварочного аппарата с открытой электрической дугой. Расположение верхнего слоя является решающим для предотвращения создания новой прогреваемой зоны. Большая часть верхнего свариваемого слоя удаляется шлифовкой.
Четвертый и последний этап состоит в восстановлении профиля рельса с помощью обычных рельсошлифовальных устройств.
Сравнительная оценка традиционного метода ручной сварки и новой методики была получена с помощью записи термической истории обоих процессов с помощью термопар. Несколько основных заключений показывают металлургическую надежность процесса.
- Несмотря на использование предпрогрева температурой всего 80°C, температуры в околошовной зоне после наложения каждого из слоев остается на уровне, превышающем 200°C, предотвращая любые трансформации структуры в мартенситную (так как температура начала этого процесса равна 160°C для рельсов класса 260).
- Скорость охлаждения в новом процессе почти идентична стандартному методу ручной сварки для всех проходов кроме первого. Более высокая скорость в 5,2 °C/с после первого прохода так же не превышает и половины критического значения преобразования в мартенсит.
- Стык наложения слоев сварки без трещин результирует в полностью перлитной микроструктуре без мартенситов и бейнитов.
- Диаграмма твердости показывает, что износостойкость бейнитных сварных слоев будет сравнима с рельсом класса R260 и обеспечит продолжительное качество профиля.
- Сварной слой был подвергнут тестированию на износ при изгибах с приложенным трехкратным усилием. Пять миллионов тестовых циклов были успешно пройдены. Тот же слой успешно выдержал затем 4,3 миллиона циклов при восьмикратной силе воздействия по сравнению со средними эксплуатационными условиями.
Следующие факторы говорят в пользу экономичности и технической эффективности нового процесса:
1. Уход от обычной температуры предпрогрева в 350°C к уровню 80°C дает преимущество быстроты ремонта, сниженной глубины околошовной зоны и более стабильной микроструктуры.
2. Использование стандартной процедуры удаления дефектного участка с помощью автоматизированного фрезерования обеспечивает повторяемость результата и устраняет субъективный фактор влияния оператора.
3. Использование полуавтоматического программируемого сварочного процесса обеспечивает точное поддержание температуры нагрева и предсказуемую длительность обработки.
Качество восстановленной таким образом рабочей поверхности гарантировано, восстановленное место обладает высокой износостойкостью, аналогичной стандартному рельсу стандарта R260 и однородной твердостью и микроструктурой.
Патентованная технология Tata Steel включает четыре шага.
Сначала дефект удаляется с помощью переносного шлифовального станка, который закрепляется на рельсе. Это обеспечивает полноценное удаление дефектного участка. Само по себе это уже является значительным улучшением по сравнению с использованием ручного шлифовального инструмента или кислородной резки, которые не обеспечивают стабильной формы выборки и качества поверхности, требуемой для автоматической сварки.
Во-вторых, место очищенного дефекта и прилегающий участок подвергается предпрогреву с помощью традиционной горелки. Для рельсов класса 260 температура предпрогрева находится в промежутке от 60 до 80°C. Выбор такого диапазона температуры дает возможность контролировать микроструктуру в прогреваемой зоне и поддерживать запрограммированную квадратную форму стыка слоев последовательных и соседних участков, обеспечивая перлитную микроструктуру в прогреваемой зоне, свободную от мартенситов, повышающих хрупкость. Такая температура подходит для основной массы современных рельсов из высокоуглеродистой стали, но возможно ее следует скорректировать для сталей с другими характеристиками, таких как низкоуглеродистые безкарбидные бейнитные стали.
Третья стадия заключается в использовании полуавтоматического сварочного аппарата с открытой электрической дугой. Расположение верхнего слоя является решающим для предотвращения создания новой прогреваемой зоны. Большая часть верхнего свариваемого слоя удаляется шлифовкой.
Четвертый и последний этап состоит в восстановлении профиля рельса с помощью обычных рельсошлифовальных устройств.
Сравнительная оценка традиционного метода ручной сварки и новой методики была получена с помощью записи термической истории обоих процессов с помощью термопар. Несколько основных заключений показывают металлургическую надежность процесса.
- Несмотря на использование предпрогрева температурой всего 80°C, температуры в околошовной зоне после наложения каждого из слоев остается на уровне, превышающем 200°C, предотвращая любые трансформации структуры в мартенситную (так как температура начала этого процесса равна 160°C для рельсов класса 260).
- Скорость охлаждения в новом процессе почти идентична стандартному методу ручной сварки для всех проходов кроме первого. Более высокая скорость в 5,2 °C/с после первого прохода так же не превышает и половины критического значения преобразования в мартенсит.
- Стык наложения слоев сварки без трещин результирует в полностью перлитной микроструктуре без мартенситов и бейнитов.
- Диаграмма твердости показывает, что износостойкость бейнитных сварных слоев будет сравнима с рельсом класса R260 и обеспечит продолжительное качество профиля.
- Сварной слой был подвергнут тестированию на износ при изгибах с приложенным трехкратным усилием. Пять миллионов тестовых циклов были успешно пройдены. Тот же слой успешно выдержал затем 4,3 миллиона циклов при восьмикратной силе воздействия по сравнению со средними эксплуатационными условиями.
Получите дополнительную информацию…