www.engineering-russia.com
28
'12
Written on Modified on
Восход суперзвезды механической обработки
Почему новая инструментальная система позволяет увеличить удельный съем металла
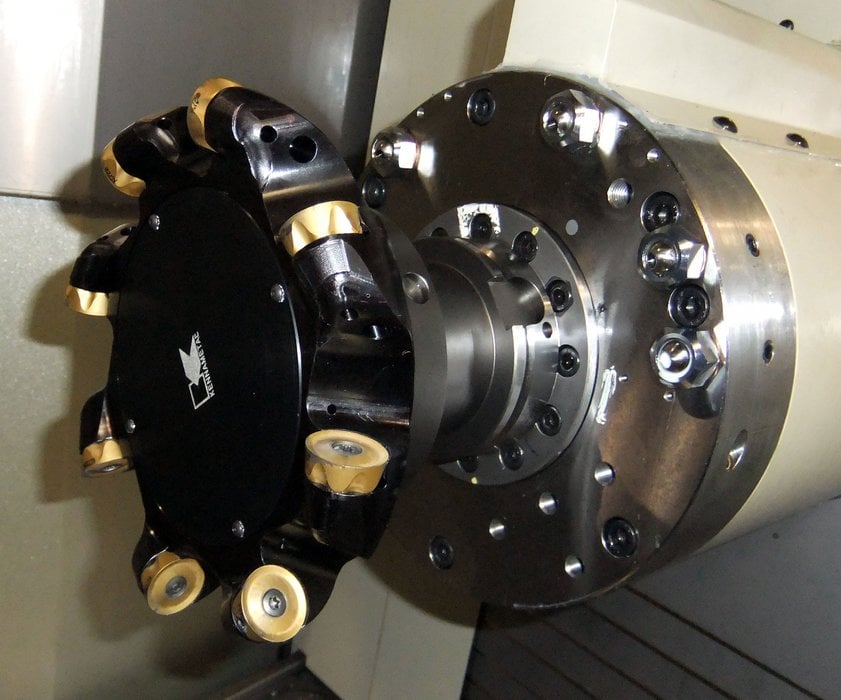
Марк Хастон, вице-президент, Отдел инженерных решений
Даг Ивалд, Директор, Отдел управления продукцией, инструментальные системы
Руй де Фрота де Соуза, начальник Отдела инструментальных систем, проектирование изделий
Компания Kennametal Inc., Латроб, Пенсильвания
Механическая обработка труднообрабатываемых материалов, таких как титан, сама по себе представляет сложную задачу. Механическая обработка подобных сплавов при дополнительной необходимости повышения производительности означает максимальное увеличение удельного съема металла в единицу времени при этом скорости резания низкие, а возникающие усилия резания весьма значительные. Станкостроительные компании предлагают специализированные токарные, фрезерные и многоцелевые центры, которые характеризуются повышенной жесткостью конструкции и усиленным шпиндельным узлом, а так же увеличенной массой станины станка при значительных габаритах, все это необходимо для минимизации нежелательных вибраций, которые ухудшают качество деталей и снижают стойкость инструмента. Несмотря на то, что эти усовершенствования способствовали повышению производительности, самым слабым местом часто было само соединение хвостовика инструмента со шпинделем.
В большинстве случаев, именно соединение шпиндель-инструмент определяет, как много материала можно снять при выполнении данной операции. Причина заключается в том, что эта зона сопряжения должна выдерживать большие нагрузки и при этом сохранять свою жесткость, пока деформация инструмента не станет слишком большой или не начнется вибрация обрабатываемой детали. При непрерывном совершенствовании режущих инструментов и обрабатывающих центров, соединение шпинделя, которое наилучшим образом использует имеющийся резерв мощности, представляет собой важный фактор, который следует учесть на ранней стадии планирования производства.
За последние несколько десятилетий были разработаны или оптимизированы несколько типов шпиндельных соединений. Благодаря выгодной цене, конус 7/24 ISO стал одной из наиболее популярных систем на рынке. Он успешно показал себя во многих областях применения, но ограничения по точности и неспособности работать на больших оборотах лишают возможности дальнейшее развитие этой системы.
Появление системы с контактом по конусу и торцу было большим шагом вперед по сравнению со стандартным конусом 7/24. Сочетание торцового контакта со сплошным конусом 7/24 обеспечивает более высокую точность в направлении оси Z, но имеет и ряд недостатков, а именно, потеря жесткости при высоких скоростях или больших изгибающих нагрузках. Большинство хвостовиков на рынке инструмента являются сплошными, а шпиндели имеют относительно низкое усилие зажима. Жесткость соединения ограничена, поскольку необходимо сводить к минимуму радиальное воздействие. Для достижения замыкания этих систем по торцу необходимо выдержать жесткие допуски на изготовление самих конусов, результатом чего являются высокие затраты на производство.
В 1985 г. компании Kennametal и Krupp WIDIA инициировали совместную программу по разработке универсальной быстросменной системы, которая теперь известна под названием KMTM и недавно была стандартизована по ISO 26622. В начале 90-х годов в Европе начали применять на станках систему HSK, которая позже стала стандартом DIN 69893, а затем - стандартом ISO 12164.
Быстросменная система инструмента KMTM состоит из двух основных узлов: зажимное устройство и режущая головка. Зажимное устройство крепится на станке (револьверная головка или резцедержатель для стационарного применения и вращающийся шпиндель для вращающегося инструмента) и является ответной частью для режущих головок и базовых держателей. При необходимости смены инструмента оператор просто разжимает механизм крепления, заменяет режущую головку и зажимает следующую в рабочем положении. Простой станка не превышает нескольких секунд.
Система KM4XTM компании Kennametal представляет собой следующее поколение серии KM. Некоторые системы способны передавать значительный крутящий момент, но усилия резания создают также изгибающие моменты, которые будут превышать допустимые значения до достижения максимального крутящего момента. При сочетании высокого усилия зажима и оптимизированной геометрии контакта, система KM4X обеспечивает надежное соединение, высочайшую жесткость и способность выдерживать высокие изгибающие нагрузки для значительного повышения рабочих характеристик при механической обработке высокопрочных сплавов и других материалов, что позволяет получить чрезвычайно высокий уровень съема металла и обработать большее число деталей за смену.
Трехкратное увеличение сопротивления изгибающему моменту
Соединение шпинделя должно выдерживать нагрузки от крутящего момента и изгибающие нагрузки, соответствующие техническим параметрам станка и требованиями повышения производительности. На операциях фрезерования кукурузными фрезами, где вылет значительно больше диаметра, становится очевидным, что ограничивающим фактором является способность зоны сопряжения хвостовика со шпинделем выдерживать изгибающие нагрузки. В качестве примера, кукурузная фреза со сменными пластинами, имеющая вылет 250 мм от торца шпинделя и диаметр 80 мм, создает изгибающий момент 4620 Нм и крутящий момент менее 900 Нм при удельном съеме 360 см3/мин во время обработки титанового сплава Ti6Al4V при ширине фрезерования 12,7 мм и припуске 63,5 мм.
Самыми важными показателями конусного соединения шпинделя с контактом по торцу являются усилие зажима и радиальное воздействие сил. При увеличении силы закрепления и оптимизации соединения можно еще больше повысить жесткость соединения.
Используя контакт по трем поверхностями для повышения жесткости и оптимизации распределения усилия зажима и посадки с натягом, разработка KM4XTM имеет своим результатом в три раза большую способность сопротивления изгибающему моменту в сравнении с другими инструментальными системами.
Это означает:
-На предприятиях можно применять оборудованные моделью KM4X высокопроизводительные станки для повышения скорости и подачи в сложных случаях механической обработки, получая таким образом 100% использования потенциала станка.
-Часто меньшее соединение KM4X, например, модель KM4X100, будет обеспечивать те же самые или даже лучшие показатели, чем соединение большего размера.
-Системы KM4X можно применять на многоцелевых токарных обрабатывающих центрах в ручном, полуавтоматическом или полностью автоматическом режиме.
По конструкции, KM4X может работать в широком диапазоне применения от низкой скорости/высокого крутящего момента до высокой скорости/низкого крутящего момента, позволяя изготовителям достигать абсолютный максимум от своего производственного оборудования.
Фрезерование, сверление и токарная обработка широкой номенклатуры материалов становятся еще более производительными!
К применению системы не предъявляется никаких особых требований. Техническую консультацию по механической обработке титана и дополнительную информацию можно получить, обратившись в компанию Kennametal или посетив сайт www.kennametal.com.
KM4X_with_cutter.jpeg: При сочетании высокого усилия зажима и оптимизированных уровней воздействия, KM4X обеспечивает надежное соединение, чрезвычайно высокую жесткость и способность выдерживать высокие изгибающие нагрузки для значительного повышения рабочих характеристик при механической обработке высокопрочных сплавов и других материалов, что позволяет повысить удельный съема металла и обработать большее число деталей за смену.
KM4X_8.jpeg: Система соединения шпинделя KM4XTM компании Kennametal имеет конфигурацию, предназначенную для тяжелых режимов работы и способную работать в условиях высоких скоростей, низкого крутящего момента или низких скоростей и высокого крутящего момента. Без системы KM4X, длинокромочная фреза при обработке превысила бы ограничения по изгибающему моменту задолго до достижения предельных значений крутящего момента.
KM4X_9.jpeg: Контакт по конусу и торцу и усилие зажима, объединенные для улучшения посадки с натягом и увеличения в три раза сопротивления изгибающему моменту по сравнению с другими системами. Смена инструментов производится быстро и просто, что сводит к минимуму время простоя станка.
Получите дополнительную информацию…