www.engineering-russia.com
23
'12
Written on Modified on
Эволюция ARPRO помогает дизайнерам автомобилей сбросить вес
С 1980-х годов поиски способов снижения веса транспортного средства и расхода топлива без ущерба для качества и безопасности узлов, проводившиеся производителями автомобилей, привели к обширному ряду разработок в сфере легковесных материалов, применяемых для создания конструкционных компонентов автомобиля.
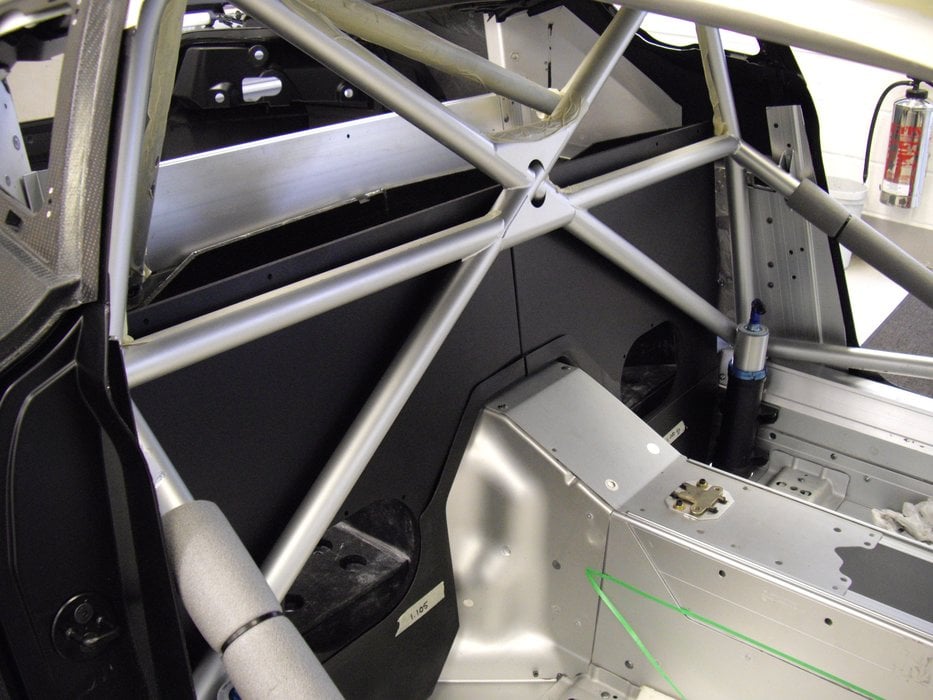
Изобретение полипропилена с пенным наполнителем вряд ли является самым важным открытием в этой области. Этот материал был впервые получен в конце 1980-х годов, а это значит, что он уже более 20 лет известен европейским автопроизводителям. В отличие от ранее применявшихся материалов, свойства поглощения энергии которых были под вопросом, полипропилен с пенным наполнителем продемонстрировал два фундаментальных физических свойства, которые сразу отнесли его в разряд «эталонного» материала для защиты от ударов на низких скоростях. Во-первых, структура пенопласта с закрытыми порами означает, что он изотропичен, т.е. обладает одинаковыми постоянными свойствами во всех направлениях, независимо от того, с какой стороны нанесен удар. Это в корне отличалось от изделий из твердого полиуретана и изделий, полученных литьем под давлением, свойства которых традиционно подгонялись под единственный сценарий столкновения. Другим преимуществом является то, что его можно многократно деформировать, но он возвращается к своей исходной форме, что идеально подходит для защиты от ударов на низких скоростях. Наличие этой особенности означает, что данный материал не только отвечает требованиям национальных и промышленных стандартов и норм, но во многих случаях превосходит их, как, например, требования по пассивной безопасности, установленные EURO NCAP (европейский комитет по проведению независимых краш-тестов авто с оценкой активной и пассивной безопасности.)
В 1990-х годах были впервые разработаны специальные марки материала, в том числе пористые материалы и материалы с дискретным удельным поверхностным сопротивлением, а также были выпущены первые партии полипропилена с пенным наполнителем разных цветов.
Конструкторы автомобилей быстро распознали возможности, предоставляемые всей линейкой материалов, и сегодня они активно применяются по всему миру. Диапазон применения простирается от изделий пассивной безопасности, таких как двери, гасители энергии бокового удара, дверные панели, подголовники, каркасы сидений, защита сидений и колен, до использования в складском хозяйстве. В последнем случае благодаря высокой удельной прочности материал может применяться для хранения комплектов инструмента, для изготовления ковриков, погрузочных платформ и компонентов конструкций. Несложно изготовить, например, настил для хранения, который будет достаточно большим, чтобы заполнить всю площадь (а значит, не будет сдвигаться при перемещении грузов), но который не добавит существенного веса, а наоборот, придаст дополнительную упругость конструкции, например, в целях поглощения энергии удара при ударе с тыльной стороны. Чтобы изготовить аналогичную вещь методом литья под давлением, потребуется дорогая оснастка, но кроме того, в результате мы получим изделие со значительным весом, которое к тому же придает заметно меньше упругости конструкции. В самом деле, сегодня полипропилен с пенным наполнителем применяется практически везде, где требования к эстетическому виду не являются превалирующими и где нет опасности длительного воздействия ультрафиолетовых лучей.
Изделия из полипропилена с пенным наполнителем также широко используются для закрепления грузов при транспортировании хрупких компонентов между заводами и сборочными производствами, сводя к минимуму процент брака при перевозке и быстро компенсируя инвестиционные затраты. Очень часто срок службы легковесных контейнеров для перевозки узлов превышает цикл производства автомобиля определенной модели. Альтернативой могут служить деревянные паллеты, которые стоят дешево, но им сложнее придать нужную форму, или стальные конструкции, которые предоставляют надежную физическую защиту, но могут повредить перевозимый груз вследствие передачи избыточных сил, вызванных вибрацией или ударами.
В некоторых сферах применения, например, при производстве сидений, общее снижение веса может достигать 35% в сравнении с альтернативными решениями, предоставляется большая гибкость дизайнерских решений для комбинированных деталей и возможность сочетания с другими материалами там, где это возможно. Затраты на оснастку заметно ниже чем при литье под давлением, при этом легковесные изделия предоставляют возможность устранить негативные свойства без необходимости дальнейших инвестиций в оснастку. В то же время, возможность создавать детали, сцепляющиеся друг с другом, предоставляют большую свободу конструирования и совместимость с другими материалами. Ярким тому примером является BMW 5-й серии, в котором материал ARPRO использован для изготовления задних сидений, что снизило затраты на оснастку, сократило время проектирования и заметно уменьшило вес сидений.
Повышенная формуемость, предоставляющая большую свободу дизайнерам, стала по сути ключевой разработкой, связанной с этим материалом, с момента его изобретения два десятилетия назад. Последние модификации материала и улучшенная оснастка расширили границы практически реализуемых 3-D моделей, а также позволили создавать более мелкие и тонкие изделия. Клиенты имеют широкий выбор марок с разной плотностью для достижения требуемого состава с минимальным расходом пара и временем цикла. Например, противосолнечные козырьки, которые, как элементы безопасности, обязательно должны проходить испытание на удар, можно без труда формовать, поскольку инновационные технологии позволяют работать с более мелкими полимерными шариками и получать тонкие детали, что в свою очередь минимизирует количество пор на финишной поверхности.
Последние разработки также привели к созданию изделий, процент брака которых заметно снижен, а также сокращено время отладки оснастки и запуска процесса изготовления партий деталей.
Продолжает быстро меняться и эстетическая составляющая изделий. Изделия, выпускаемые сегодня, имеют поверхность, которая уже не напоминает «сырой» материал, а представляет собой гладкую однородную текстуру. Это играет ключевую роль в снижении количества и веса компонентов и не в последнюю очередь в оформлении тех скрытых участков, где ограниченная досягаемость ультрафиолетовых лучей позволяет оставлять эти участки незащищенными.
Появление электромобилей определило еще одну возможность применения материала, т.к. минимизация веса этого транспортного средства является критичной для продления ресурса аккумулятора. С этой целью в 2010 году была создана новая многослойная технология, известная под названием inrekor, в основе которой лежит материал ARPRO с приклеенными внешними защитными слоями, что придает исключительную прочность под нагрузкой. Прочность и упругость материала inrekor позволяют использовать его для изготовления деталей ходовой части, которая традиционно является наибольшей составляющей веса автомобиля. Впервые появилась возможность обеспечить легковесность электромобиля, чтобы он стал действительно альтернативным транспортным средством.
Ключевым моментом в использовании легковесных структурных компонентов, конечно, является возможность убедить конструкторов, производителей и потребителей автомобилей в том, что этот материал является достаточно прочным, надежным и безопасным. Однако прочность и сопротивление изгибу материала inrekor экспоненциально растет с увеличением толщины стержневой основы, что снимает всяческие сомнения в его надежности. В то же время, присущая материалу способность «интеллектуальной» интеграции функций – изоляции, разделения, создания воздушных каналов – а также наличие встроенных монтажных точек, означает, что легковесное и экономически эффективное решение может быть достигнуто с минимальными капитальными вложениями. Крепление конечного изделия тоже не представляет сложности: в отличие от изделий из ячеистых материалов детали из материала inrekor можно приклепывать, приклеивать, приваривать точечной сваркой или присоединять механическим креплением в зависимости от особенностей применения.
Изотропическая природа стержневой основы ARPRO внутри оболочки из материала inrekor обеспечивает быстрое рассеивание энергии удара во всех направлениях. Нет сомнения в том, что автопроизводителей удалось убедить в достоинствах материала inrekor после того, как инновационные модели электромобилей стали выпускаться с рамой, изготовленной из этого материала.
Например, в типовом четырехместном автомобиле вес рамы можно снизить с 300 до 160 кг, что весьма существенно, т.к. каждый «сэкономленный» килограмм веса увеличивает ресурс аккумулятора на 3-4 км. (Кроме того, по оценкам экспертов использование данной технологии в бензиновых и дизельных автомобилях по всему миру позволило бы ежегодно экономить до 10 миллиардов (!) литров топлива.)
Гибкость многослойной технологии и разработка соответствующих методов и изделий означает, что внешние слои из разных материалов могут быть приклеены к стержневой основе в зависимости от назначения изделия и требования к его внешнему виду. В то же время, можно легко внести изменения в конструкцию изделия с применением минимальной оснастки и капиталовложений, поскольку вместо того, чтобы вырезать детали из готовых сэндвич-панелей на станке с ЧПУ, вырезается основа с помощью водяной струи по трафарету внешнего слоя, полученному лазерной резкой -несомненное преимущество, когда скорость имеет значение. При этом оба материала поддаются традиционной вырубке на прессе или на штамповочной машине. Одним из последних примеров является создание специального топливного бака с оболочкой из материала inrekor для гоночного автомобиля Aston Martin, что не только обеспечивает жесткое крепление в защитной дуге, но также отвечает требованиям минимальной толщины оболочки в 10 мм. При этом скорость создания деталей с нуля лучше всего подтверждается тем фактом, что от первоначального проекта до реального применения готовой рамы из материала inrekor в автомобиле Speedster 356 прошло всего 13 недель.
Гибкость применения легковесных материалов приобретает еще большее значение с учетом разницы веса рам в автомобилях разных моделей, где стержневые основы разной плотности рассчитываются под определенный вес каждой модели.
Не только уменьшенный вес, но и гибкость современных многослойных технологий и легковесных изделий, таких как полипропилен с пенным наполнителем ARPRO и inrekor, позволяют успешно использовать эти изделия и технологии для уменьшения веса в самых разных сферах применения как сегодня, так и в ближайшей перспективе.

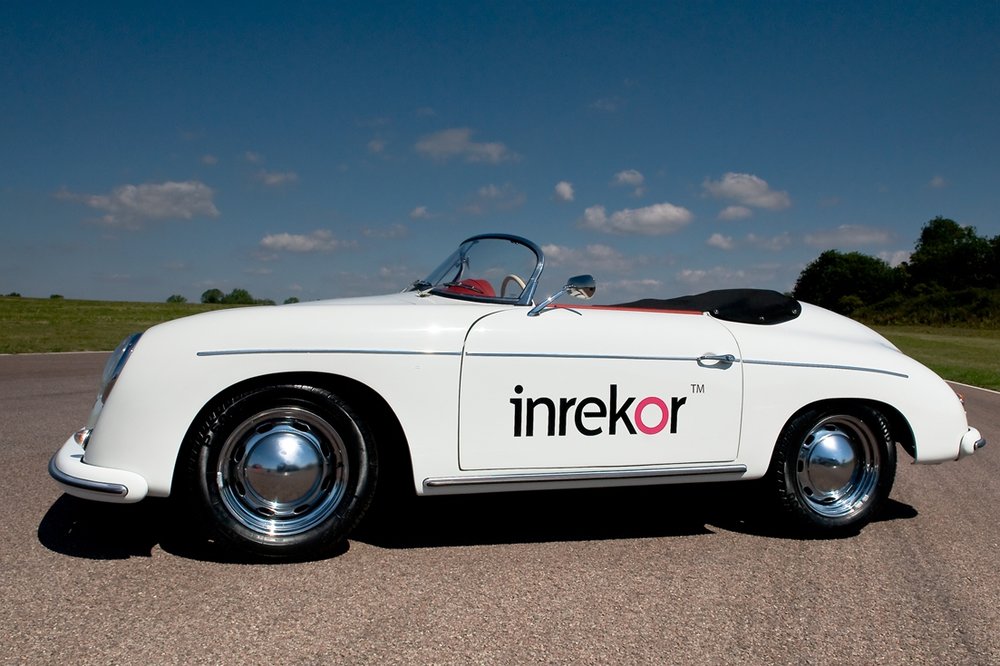
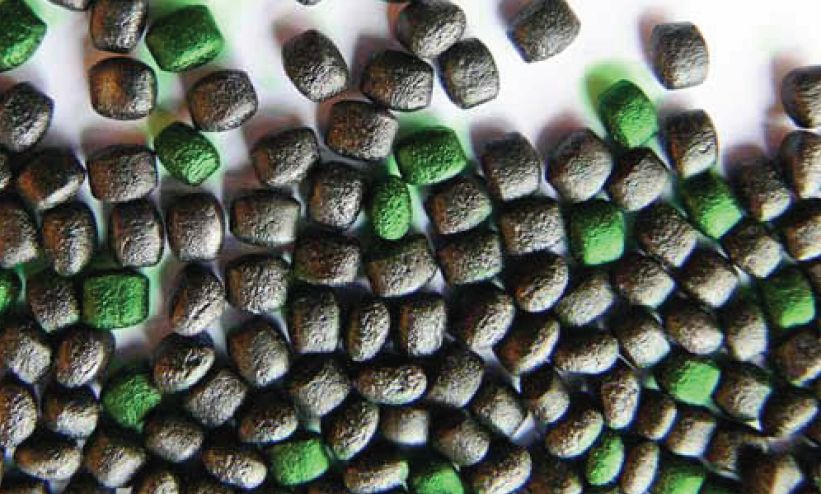
Получите дополнительную информацию…